The Project
HYPER aims to help transform H2O2 production from a large-volume, energy intensive chemical process to a smaller-scale, robust, modular, sustainable, electrochemical process, providing significant benefits.
Traditional H202 Production Drawbacks
The established production route of H2O2 is the auto oxidation of anthraquinone process (AO process).
Uses natural gas both as feedstock and energy source.
More than 95 % of H2O2 utilised today still comes from this traditional AO process.
H2O2 is produced far from where it is needed, high concentrations are hard to transport, and low concentrations, being mostly water, are uneconomical to ship.
Hydrogen (H2) is produced by the steam methane reforming (SMR) process – H2 production from SMR has a significant CO2 footprint.
The use of H2O2 stabilisers requires extra processing steps in downstream applications.
The AO process needs a Pd catalyst, including processing steps for recovery and reactivation.
The current AO processes requires a cocktail of aromatic hydrocarbon and polar, fossil-fuel derived solvents (phosphates, long-chain alcohols or alkyl ureas).
Benefits of HYPER
The HYPER method is modular, robust, on-site, allowing on-demand H2O2 production – removing concerns about decomposition, shipping and the use of stabilisers, thus providing exact concentrations as needed, simplifying downstream applications.
The electrochemical process is catalyst-free, eliminating the need for use and recovery of expensive Pd, a critical raw material, and does not involve critical raw materials as electrodes.
The electrochemical process will be run in aqueous electrolytes and the H2O2 production will take place in water with no organic solvent requirements, improving the environmental footprint for H2O2 production.
HYPER uses water as a solvent, electrolyte and feedstock, and electricity as the energy source, which improves the process sustainability and scalability.
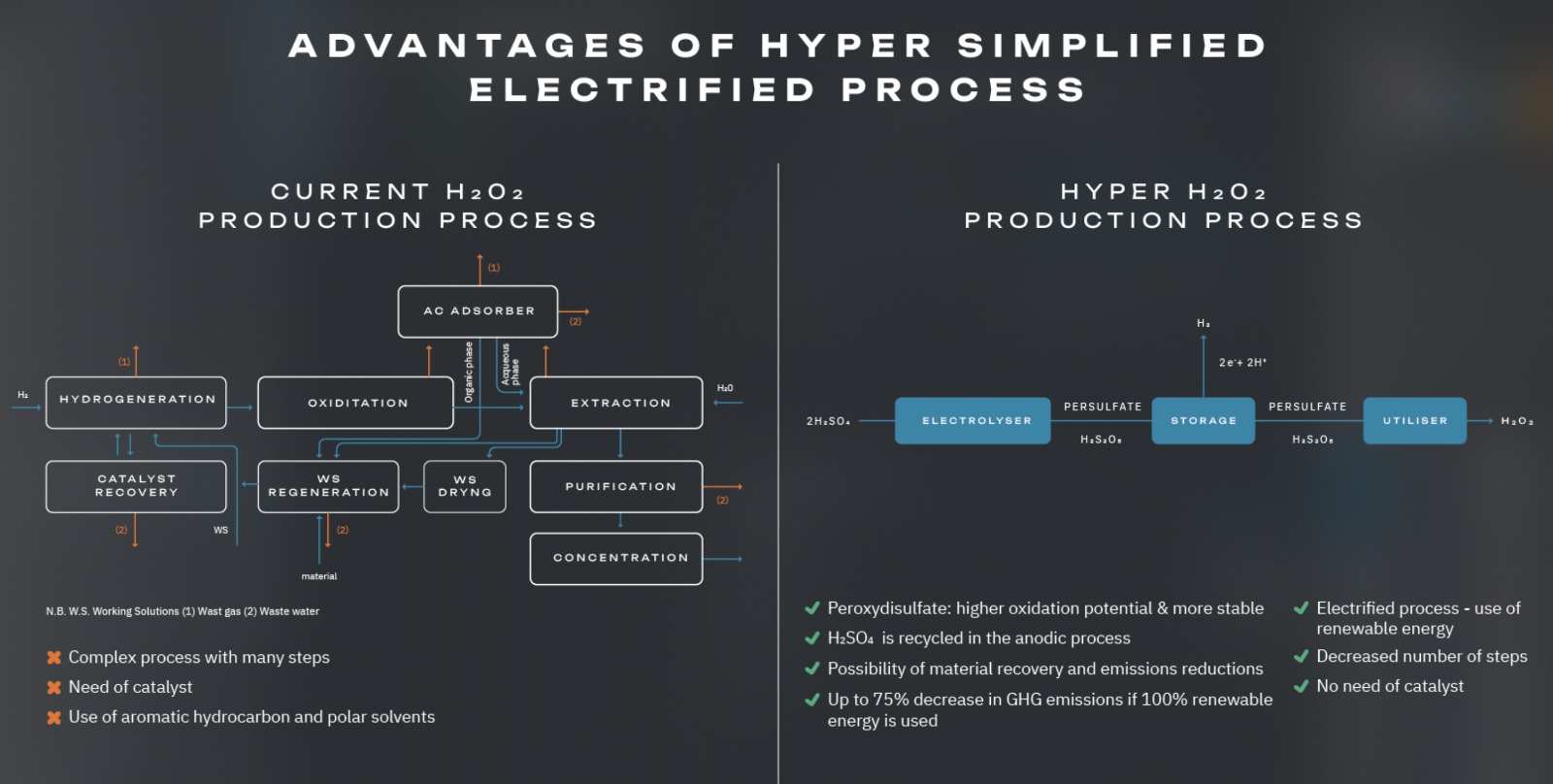